¿QUÉ ES EL ANALISIS DE RIESGOS, IDENTIFICACIÓN Y CONTROL DE PUNTOS CRÍTICOS (ARICPC)?
surge en la década de los sesenta como un método para controlar los alimentos que destinados a usarse en los programas espaciales. La aplicación de este método debía garantizar la seguridad de los alimentos que consumirían los astronautas
El método se desarrolló en Estados Unidos de América, participaron la Corporación Pillsbury, la Armada Naval de los Estados Unidos y la Agencia Nacional Aeroespacial (NASA)
El método proporciona una metodología que se enfoca a cómo deben evitarse o reducirse los peligros asociados con la producción de alimentos , evaluación cuidadosa de todos los factores internos y externos que intervienen en el proceso de un alimento las etapas usadas en la aplicación del método:
1. Formar un equipo de Análisis de Riesgos, Identificación y Control de Puntos Críticos
2. Describir el alimento y su distribución
3. Identificar el uso del alimento por los consumidores
4. Elaborar un diagrama de flujo
5. Verificar el diagrama de flujo
6. Enumerar los riesgos asociados con cada operación del proceso y las medidas preventivas para controlar los mismos
7. Identificar en cada operación de proceso los puntos críticos de control
8. Establecer las especificaciones para cada punto crítico de control
9. Establecer un procedimiento de monitoreo para cada punto crítico de control
10. Establecer las acciones correctivas
11. Establecer los procedimientos de registro y documentación de la aplicación del método de Análisis de Riesgos, Identificación y Control de Puntos Críticos
12. Verificar el método de Análisis de Riesgos, Identificación y Control de Puntos Críticos.
VENTAJAS EN EL SISTEMA
Ofrece un alto nivel de calidad sanitaria a los alimentos.
Contribuye a consolidar la imagen y credibilidad de la empresa frente a los consumidores y
Aumenta la competitividad tanto en el mercado interno como en el externo.
Contribuye a la reducción de costos y a disminuir sustancialmente la destrucción o reproceso de productos, lo que resulta en un aumento de la productividad.
Genera ganancias institucionales; la autoestima e importancia del trabajo en equipo; ya que las personas involucradas pasan a un estado de conciencia, ganando autoconfianza y satisfacción de que la producción de alimentos se realiza con un alto nivel de seguridad.
En el aspecto legal la implantación del sistema ARICPC facilita la comunicación de las empresas con la autoridad sanitaria.
Actualmente la instrumentación del ARICPC únicamente es obligatorio en la industria procesadora de productos pesqueros.
DIFICULTADES PARA SU IMPLANTACION
Las creencias y valores arraigados en algunas empresas y personas.
No considerar el costo de implantación del sistema y el tiempo en el que se empiezan a percibir los resultados.
COMO Y DONDE UTILIZAR EL SISTEMA ARICPC
El sistema ARICPC es aplicable a todo proceso de alimentos, desde la producción primaria hasta el consumo final
Los principios que integran el sistema son aplicables a cualquier actividad relacionada con los alimentos, sin embargo, un plan de ARICPC es específico para un determinado proceso.
Toda persona que participa en el proceso productivo debe estar involucrado en la implantación de los principios del sistema ARICPC
AREAS DE APLICACION
Se centra en las condiciones peligrosas en un producto o proceso como:
Contaminación
Desarrollo, supervivencia o eliminación de microorganismos
PREMISAS IMPRECINDIBLES
• Que la naturaleza de los peligros, cuya eliminación o reducción a un nivel aceptable sea considerada como esencial para la producción de alimentos inocuos.
• El valor de alcanzar la calidad sanitaria del alimento con respecto al costo de alcanzarla.
La determinación de un objetivo que conduzca a decidir la calidad aceptable y que deberá gobernar el diseño del proceso
Dado que en México su uso es muy reducido se procera con un ejemplo para ilustrarlo de una mejor manera
FUENTES DE INFORMACION
http://genesis.uag.mx/posgrado/revistaelect/calidad/cal009.htm 29/03/07
http://www.salud.gob.mx/unidades/cdi/documentos/analisis.html
http://bvs.sld.cu/revistas/ali/vol10_2_96/ali06296.htm 21/09/05
Revista Científica UDO Agrícola Volumen 4. Número 1. Año 2004. Páginas: 72-79
lunes, 15 de junio de 2009
sábado, 13 de junio de 2009
Normalización
La normalización o estandarización es la redacción y aprobación de normas que se establecen para garantizar el acoplamiento de elementos construidos independientemente, así como garantizar el repuesto en caso de ser necesario, garantizar la calidad de los elementos fabricados y la seguridad de funcionamiento.
La normalización es el proceso de elaboración, aplicación y mejora de las normas que se aplican a distintas actividades científicas, industriales o económicas con el fin de ordenarlas y mejorarlas.
Según la ISO (International Organization for Standarization) la Normalización es la actividad que tiene por objeto establecer, ante problemas reales o potenciales, disposiciones destinadas a usos comunes y repetidos, con el fin de obtener un nivel de ordenamiento óptimo en un contexto dado, que puede ser tecnológico, político o económico.
La normalización persigue fundamentalmente tres objetivos:
1. Simplificación: Se trata de reducir los modelos quedándose únicamente con los más necesarios.
2. Unificación: Para permitir la intercambiabilidad a nivel internacional.
3. Especificación: Se persigue evitar errores de identificación creando un lenguaje claro y preciso.
Normalización de la Calidad
1. La capacidad de un producto o servicio para satisfacer necesidades y expectativas explícitas e implícitas de los clientes a través de normas de productos y servicios.
2. La capacidad de una organización para suministrar de manera consistente un producto o servicio que satisface esas necesidades y expectativas a través de normas y especificaciones técnicas tales como:
ISO 9001:2008 Quality management systems -Requirements.
ISO/TS-16949 Quality management systems - Particular requirements for the application of ISO 9001:2000 for automotive production and relevant service part organizations.
QS-9000 Quality system requirements.
EAQF Evaluation d'aptitude qualité fournisseurs.
VDA6.1 Verband der Automobilindustrie, etc.
Observe que de nada sirve contar con la certificación de un producto o servicio, si la organización no posee la capacidad para poder suministrar de manera consistente, productos y servicios que cumplan con sus respectivas normas.
De hecho, muchos de los esquemas de certificación de productos y servicios requieren que la organización opere con un sistema de gestión de la calidad para evaluar tal capacidadde la organización.
Bibliografías
http://www.sayce.com.mx/index.php?id=27
http://es.wikipedia.org/wiki/Normalizaci%C3%B3n
La normalización es el proceso de elaboración, aplicación y mejora de las normas que se aplican a distintas actividades científicas, industriales o económicas con el fin de ordenarlas y mejorarlas.
Según la ISO (International Organization for Standarization) la Normalización es la actividad que tiene por objeto establecer, ante problemas reales o potenciales, disposiciones destinadas a usos comunes y repetidos, con el fin de obtener un nivel de ordenamiento óptimo en un contexto dado, que puede ser tecnológico, político o económico.
La normalización persigue fundamentalmente tres objetivos:
1. Simplificación: Se trata de reducir los modelos quedándose únicamente con los más necesarios.
2. Unificación: Para permitir la intercambiabilidad a nivel internacional.
3. Especificación: Se persigue evitar errores de identificación creando un lenguaje claro y preciso.
Normalización de la Calidad
1. La capacidad de un producto o servicio para satisfacer necesidades y expectativas explícitas e implícitas de los clientes a través de normas de productos y servicios.
2. La capacidad de una organización para suministrar de manera consistente un producto o servicio que satisface esas necesidades y expectativas a través de normas y especificaciones técnicas tales como:
ISO 9001:2008 Quality management systems -Requirements.
ISO/TS-16949 Quality management systems - Particular requirements for the application of ISO 9001:2000 for automotive production and relevant service part organizations.
QS-9000 Quality system requirements.
EAQF Evaluation d'aptitude qualité fournisseurs.
VDA6.1 Verband der Automobilindustrie, etc.
Observe que de nada sirve contar con la certificación de un producto o servicio, si la organización no posee la capacidad para poder suministrar de manera consistente, productos y servicios que cumplan con sus respectivas normas.
De hecho, muchos de los esquemas de certificación de productos y servicios requieren que la organización opere con un sistema de gestión de la calidad para evaluar tal capacidadde la organización.
Bibliografías
http://www.sayce.com.mx/index.php?id=27
http://es.wikipedia.org/wiki/Normalizaci%C3%B3n
“Reaccion en cadena, calidad, productividad, reduccion de costes y conquista del mercado”
REACCION EN CADENA CALIDAD-PRODUCTIVIDAD
En América la tradición dice que la calidad y la productividad son incompatibles: que no se pueden tener ambas. Un director de planta diría normalmente que lo uno o lo otro. A lo largo de su experiencia si se hace avanzar a la producción, se resiente la calidad. Esto será lo que le ocurra cuando no sabe como es la calidad ni como conseguirla.
Al mejorar la calidad se transfieren las horas- hombre y las horas-maquina malgastadas a la fabricación de producto bueno y a dar un servicio mejor. El resultado es una reacción en cadena: se reducen los costos, se es más competitivo, la gente esta más contenta con su trabajo, hay trabajo y más trabajo.
Los directivos de muchas compañías de Japón observaron en 1948 y 1949 que el mejorar la calidad engendra de manera natural e inevitable la mejora de la productividad.
Como resultado de la visita de un experto extranjero en el verano de 1950, la siguiente reacción en cadena quedo grabada en Japón como un estilo de vida. Esta reacción en cadena estaba en todas las pizarras de todas las reuniones con los directivos japoneses desde julio de 1950 en adelante.
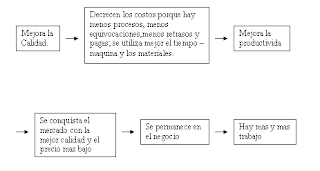
Una vez que los directivos adoptaron la reacción en cadena en Japón a partir de 1950, todos tenían un objetivo en común, es decir , la calidad.
El consumidor es la pieza más importante de la línea de producción. La calidad se debe orientar a las necesidades del consumidor, presente y futuro.

Conway implemento el control estadistico logrando que los ingenieros y los quimicos de la empresa se volvieran mas creativos para modificar el contenido del material de revestimiento del papel y asi utilizar cada vez menos, logrando un ahorro anual de $100,000 en la empresa, no cabe duda que el control estadistico abrio las puertas a la innovación en la ingenieria y en la calidad.
Como decia Philip Crosby, la calidad no cuesta, lo que cuesta es la no calidad, de hecho una empresa dedicaba le 21% de la mano de obra en corregir los productos defectuosos y gastaba un 42% del presupuesto en hacer dichos productos y repararlos.
Por ultimo cabe destacar que la medida de la productividad no hace mejorar la productividad debido a que esta medida es como la estadistica, te dicen cuantos muertos hay en un accidente automovilistico pero no dicen como prevenirlo. Sin embargo puede ser mucha ayuda para la direccion para decidir si las actividades realizadas en la empresa son coherentes con el objetivo o no y en dicho caso corregir los errores.
La calidad y la productividad si son compatibles porque todo el ser humano tendemos a mejorar día con día, tratando de hacer las cosas mejor y mas rápido, por lo tanto si uno hace las cosas bien a la primera vez después se le facilitara el trabajo por lo que tendrá mas productividad en la empresa. Ademas para producir un producto de calidad, todos los factores cuentan desde conseguir las maquinarias apropiadas con la mayor eficiencia y al menor costo posible, hasta la capacitacion del empleado para realizar bien su trabajo.
REFERENCIAS
• Walter Edward Deming
• Calidad, Productividad y Competitividad
“La salida de la crisis”
Capitulo 1
Ensayo Capitulo 1 “Reaccion en cadena, calidad, productividad, reduccion de costes y conquista del mercado”
En América la tradición dice que la calidad y la productividad son incompatibles: que no se pueden tener ambas. Un director de planta diría normalmente que lo uno o lo otro. A lo largo de su experiencia si se hace avanzar a la producción, se resiente la calidad. Esto será lo que le ocurra cuando no sabe como es la calidad ni como conseguirla.
Al mejorar la calidad se transfieren las horas- hombre y las horas-maquina malgastadas a la fabricación de producto bueno y a dar un servicio mejor. El resultado es una reacción en cadena: se reducen los costos, se es más competitivo, la gente esta más contenta con su trabajo, hay trabajo y más trabajo.
Los directivos de muchas compañías de Japón observaron en 1948 y 1949 que el mejorar la calidad engendra de manera natural e inevitable la mejora de la productividad.
Como resultado de la visita de un experto extranjero en el verano de 1950, la siguiente reacción en cadena quedo grabada en Japón como un estilo de vida. Esta reacción en cadena estaba en todas las pizarras de todas las reuniones con los directivos japoneses desde julio de 1950 en adelante.
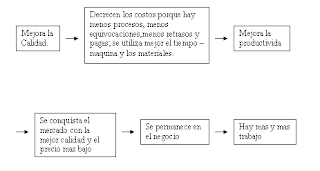
Una vez que los directivos adoptaron la reacción en cadena en Japón a partir de 1950, todos tenían un objetivo en común, es decir , la calidad.
El consumidor es la pieza más importante de la línea de producción. La calidad se debe orientar a las necesidades del consumidor, presente y futuro.

Conway implemento el control estadistico logrando que los ingenieros y los quimicos de la empresa se volvieran mas creativos para modificar el contenido del material de revestimiento del papel y asi utilizar cada vez menos, logrando un ahorro anual de $100,000 en la empresa, no cabe duda que el control estadistico abrio las puertas a la innovación en la ingenieria y en la calidad.
Como decia Philip Crosby, la calidad no cuesta, lo que cuesta es la no calidad, de hecho una empresa dedicaba le 21% de la mano de obra en corregir los productos defectuosos y gastaba un 42% del presupuesto en hacer dichos productos y repararlos.
Por ultimo cabe destacar que la medida de la productividad no hace mejorar la productividad debido a que esta medida es como la estadistica, te dicen cuantos muertos hay en un accidente automovilistico pero no dicen como prevenirlo. Sin embargo puede ser mucha ayuda para la direccion para decidir si las actividades realizadas en la empresa son coherentes con el objetivo o no y en dicho caso corregir los errores.
La calidad y la productividad si son compatibles porque todo el ser humano tendemos a mejorar día con día, tratando de hacer las cosas mejor y mas rápido, por lo tanto si uno hace las cosas bien a la primera vez después se le facilitara el trabajo por lo que tendrá mas productividad en la empresa. Ademas para producir un producto de calidad, todos los factores cuentan desde conseguir las maquinarias apropiadas con la mayor eficiencia y al menor costo posible, hasta la capacitacion del empleado para realizar bien su trabajo.
REFERENCIAS
• Walter Edward Deming
• Calidad, Productividad y Competitividad
“La salida de la crisis”
Capitulo 1
Ensayo Capitulo 1 “Reaccion en cadena, calidad, productividad, reduccion de costes y conquista del mercado”
DEFINICIONES
1. ¿Que es la calidad?
La calidad solo puede definirse en función del sujeto que juzga la calidad.
En la mente del operario, el fabrica calidad si puede estar orgulloso de su trabajo. Para el la mala calidad supone perdida del negocio, y quizás de su trabajo. La buena calidad, piensa el hará que la compañía siga en el negocio. Todo esto es cierto tanto en las empresas de servicio como en las de fabricación.
Para el gerente de planta, la calidad significa sacar los números y cumplr las especificaciones. Su trabajo también consiste en mejorar continuamente los procesos y en mejorar continuamente el liderazgo.
El consumidor, la pieza mas importante en la línea de producción.
2. Aseguramiento de la Calidad
Modelo planificado y sistemático de todas las acciones necesarias para proporcionar una confianza o seguridad adecuada de que el elemento o producto está conforme a los requisitos técnicos establecidos (..una de las normas para asegurar es la ISO 9000…)
- Búsqueda de la conformidad en productos y procesos
- Sistemas de calidad
- Prevención de errores
- Documentación de procedimientos de trabajo
- Énfasis enel diseño de productos
3. Control de la Calidad
a.- “Aquellas acciones del Aseguramiento de la Calidad que proporcionan un medio para controlar y medir las características de un elemento, proceso o facilidad respecto a los requisitos establecidos”.
Control de Calidad
b.- “Conjunto de técnicas y actividades de carácter operativo, utilizadas para verificar los requerimientos relativos a la calidad del producto o servicio”.
4. Gestión de la Calidad
“Aspecto de la función de gestión que determina y aplica la política de la calidad, los objetivos y las responsabilidades y que lo realiza con medios tales como la planificación de la calidad, el control de la calidad, la garantía de calidad y la mejora de la calidad”.
La gestión de la calidad es responsabilidad de todos los niveles ejecutivos, pero debe estar guiada por la alta dirección. Su realización involucra a todos los miembros de la organización.
5. La Calidad Total
Es el estadio más evolucionado dentro de las sucesivas transformaciones que ha sufrido el término Calidad a lo largo del tiempo. En un primer momento se habla de Control de Calidad, primera etapa en la gestión de la Calidad que se basa en técnicas de inspección aplicadas a Producción. Posteriormente nace el Aseguramiento de la Calidad, fase que persigue garantizar un nivel continuo de la calidad del producto o servicio proporcionado. Finalmente se llega a lo que hoy en día se conoce como Calidad Total, un sistema de gestión empresarial íntimamente relacionado con el concepto de Mejora Continua y que incluye las dos fases anteriores. Los principios fundamentales de este sistema de gestión son los siguientes:
Consecución de la plena satisfacción de las necesidades y expectativas del cliente (interno y externo).
Desarrollo de un proceso de mejora continua en todas las actividades y procesos llevados a cabo en la empresa (implantar la mejora continua tiene un principio pero no un fin).
Total compromiso de la Dirección y un liderazgo activo de todo el equipo directivo.
Participación de todos los miembros de la organización y fomento del trabajo en equipo hacia una Gestión de Calidad Total.
Involucración del proveedor en el sistema de Calidad Total de la empresa, dado el fundamental papel de éste en la consecución de la Calidad en la empresa.
Identificación y Gestión de los Procesos Clave de la organización, superando las barreras departamentales y estructurales que esconden dichos procesos.
Toma de decisiones de gestión basada en datos y hechos objetivos sobre gestión basada en la intuición. Dominio del manejo de la información.
6. Control Total de Calidad
Se refiere al énfasis de calidad que enmarca la organización entera, desde el proveedor hasta el consumidor. La administración de la calidad total enfatiza el compromiso administrativo de llevar una dirección continua y extenderla a toda la empresa, hacia toda la excelencia en todos los aspectos de los productos y servicios que son importantes para el cliente.
7. Validación
Validar un proceso consiste en realizar sistemáticamente los procesos de puesta a punto del mismo, así tendremos las fases:
• Planificación. Estableceremos programas temporales y listas de verificación - protocolos de nuestra validación con criterios de aceptación/rechazo, necesidades de recursos, análisis de riesgos,... Esta planificación nos ahorrara mucho tiempo y esfuerzos en vano, hay que cuidarla.
• IQ - Cualificación de la instalación. Esta fase va asociada a la instalación por parte de nuestro proveedor del sistema e incluirá la calibración de los elementos de medición y control, la documentación, planos, instrucciones de trabajo, la cualificación y formación del equipo de validación...
• OQ - Cualificación operativa. Esta es la fase crucial de puesta a punto de nuestro proceso donde debe probarse su robustez y fiabilidad frente a casos peores. Es crítico aquí el diseño de experimentos para desafiar al proceso.
• PQ - Cualificación de prestaciones o funcional. En esta última fase se verá la repetitividad y reproducibilidad de nuestro proceso. La formación y cualificación precisa para su operación, instrucciones de trabajo definitivas, puestas en marcha, paradas, ... .
8. Inspección
La disposición de un lote puede determinarse inspeccionando cada unidad ("inspección al 100%") o inspeccionando una muestra o porción del lote.
9. Muestreo Aleatorio
Consideremos una población finita, de la que deseamos extraer una muestra. Cuando el proceso de extracción es tal que garantiza a cada uno de los elementos de la población la misma oportunidad de ser incluidos en dicha muestra, denominamos al proceso de selección muestreo aleatorio.
El muestreo aleatorio se puede plantear bajo dos puntos de vista:
• Sin reposición de los elementos;
• Con reposición
10. Muestreo Aleatorio Estratificado
Un muestreo aleatorio estratificado es aquel en el que se divide la población de N individuos, en k subpoblaciones o estratos, atendiendo a criterios que puedan ser importantes en el estudio, de tamaños respectivos N1, ..., Nk, y realizando en cada una de estas su poblaciones muestreos aleatorios simples de tamaño ni.

11. Muestreo Sistematico
En este caso se elige el primer individuo al azar y el resto viene condicionado por aquél. Este método es muy simple de aplicar en la práctica y tiene la ventaja de que no hace falta disponer de un marco de encuesta elaborado. Puede aplicarse en la mayoría de las situaciones, la única precaución que debe tenerse en cuenta es comprobar que la característica que estudiamos no tenga una periodicidad que coincida con la del muestreo (por ejemplo elegir un día de la semana para tomar muestras en un matadero, ya que muchos ganaderos suelen sacrificar un día determinado).

12. Auditoria de calidad
La auditoría de calidad es una herramienta de gestión empleada para verificar y evaluar las actividades relacionadas con la calidad en el seno de una organización. Su realización se inicia en una o varias de las situaciones siguientes:
Por solicitud de la Administración: la Administración puede someter a auditoría el sistema de gestión de la calidad de un centro de fabricación como una medida más dentro del proceso de homologación de un producto.
Por exigencia de un cliente: Un cliente puede exigir la auditoría del sistema de calidad del suministrador antes de iniciar o durante el desarrollo .
Por solicitud a una entidad de certificación: Cualquier organización puede solicitar la certificación de que su sistema de calidad es conforme al modelo adoptado y, en consecuencia, someterse a una auditoría.
Por exigencia del sistema de calidad propio: Según cual sea el modelo de gestión de la calidad adoptado, las auditorías internas se realizarán por personal interno con una regularidad periódica.
13. Prueba.
El efecto de proporcionar suficientes evidencias para persuadir al cliente o consumidor que el producto es de buena calidad
14. Control estadístico de procesos
El Control Estadístico de Procesos (C.E.P.), también conocido por sus siglas en inglés "SPC" es un conjunto de herramientas estadísticas que permiten recopilar, estudiar y analizar la información de procesos repetitivos para poder tomar decisiones encaminadas a la mejora de los mismos, es aplicable tanto a procesos productivos como de servicios siempre y cuando cumplan con dos condiciones: Que se mensurable (observable) y que sea repetitivo (Curso Teórico- Práctico CEP, 2004). El propósito fundamental de C.E.P. es identificar y eliminar las causas especiales de los problemas (variación) para llevar a los procesos nuevamente bajo control.
15. Defecto
Carencia de alguna cualidad propia de un producto o servicio.
16. No conformidad
Es un incumplimiento de los requisitos definidos (por el Sistema de Calidad y Medioambiente, por la ley, por las especificaciones del centro o de la Institución, etc.)
REFERENCIAS:
http://www.unap.cl/public/01%20Calidad%20Concepto%20y%20Definiciones.pdf
http://www.tecno-med.es/validacion_de_procesos.htm
http://www.estrucplan.com.ar/Producciones/Entrega.asp?identrega=438
http://www.bioestadistica.uma.es/libro/node88.htm
http://minnie.uab.es/~veteri/21216/TiposMuestreo1.pdf
http://sistemas.itlp.edu.mx/tutoriales/produccion1/tema2_7.htm
http://www.monografias.com/trabajos11/conge/conge.shtml
La calidad solo puede definirse en función del sujeto que juzga la calidad.
En la mente del operario, el fabrica calidad si puede estar orgulloso de su trabajo. Para el la mala calidad supone perdida del negocio, y quizás de su trabajo. La buena calidad, piensa el hará que la compañía siga en el negocio. Todo esto es cierto tanto en las empresas de servicio como en las de fabricación.
Para el gerente de planta, la calidad significa sacar los números y cumplr las especificaciones. Su trabajo también consiste en mejorar continuamente los procesos y en mejorar continuamente el liderazgo.
El consumidor, la pieza mas importante en la línea de producción.
2. Aseguramiento de la Calidad
Modelo planificado y sistemático de todas las acciones necesarias para proporcionar una confianza o seguridad adecuada de que el elemento o producto está conforme a los requisitos técnicos establecidos (..una de las normas para asegurar es la ISO 9000…)
- Búsqueda de la conformidad en productos y procesos
- Sistemas de calidad
- Prevención de errores
- Documentación de procedimientos de trabajo
- Énfasis enel diseño de productos
3. Control de la Calidad
a.- “Aquellas acciones del Aseguramiento de la Calidad que proporcionan un medio para controlar y medir las características de un elemento, proceso o facilidad respecto a los requisitos establecidos”.
Control de Calidad
b.- “Conjunto de técnicas y actividades de carácter operativo, utilizadas para verificar los requerimientos relativos a la calidad del producto o servicio”.
4. Gestión de la Calidad
“Aspecto de la función de gestión que determina y aplica la política de la calidad, los objetivos y las responsabilidades y que lo realiza con medios tales como la planificación de la calidad, el control de la calidad, la garantía de calidad y la mejora de la calidad”.
La gestión de la calidad es responsabilidad de todos los niveles ejecutivos, pero debe estar guiada por la alta dirección. Su realización involucra a todos los miembros de la organización.
5. La Calidad Total
Es el estadio más evolucionado dentro de las sucesivas transformaciones que ha sufrido el término Calidad a lo largo del tiempo. En un primer momento se habla de Control de Calidad, primera etapa en la gestión de la Calidad que se basa en técnicas de inspección aplicadas a Producción. Posteriormente nace el Aseguramiento de la Calidad, fase que persigue garantizar un nivel continuo de la calidad del producto o servicio proporcionado. Finalmente se llega a lo que hoy en día se conoce como Calidad Total, un sistema de gestión empresarial íntimamente relacionado con el concepto de Mejora Continua y que incluye las dos fases anteriores. Los principios fundamentales de este sistema de gestión son los siguientes:
Consecución de la plena satisfacción de las necesidades y expectativas del cliente (interno y externo).
Desarrollo de un proceso de mejora continua en todas las actividades y procesos llevados a cabo en la empresa (implantar la mejora continua tiene un principio pero no un fin).
Total compromiso de la Dirección y un liderazgo activo de todo el equipo directivo.
Participación de todos los miembros de la organización y fomento del trabajo en equipo hacia una Gestión de Calidad Total.
Involucración del proveedor en el sistema de Calidad Total de la empresa, dado el fundamental papel de éste en la consecución de la Calidad en la empresa.
Identificación y Gestión de los Procesos Clave de la organización, superando las barreras departamentales y estructurales que esconden dichos procesos.
Toma de decisiones de gestión basada en datos y hechos objetivos sobre gestión basada en la intuición. Dominio del manejo de la información.
6. Control Total de Calidad
Se refiere al énfasis de calidad que enmarca la organización entera, desde el proveedor hasta el consumidor. La administración de la calidad total enfatiza el compromiso administrativo de llevar una dirección continua y extenderla a toda la empresa, hacia toda la excelencia en todos los aspectos de los productos y servicios que son importantes para el cliente.
7. Validación
Validar un proceso consiste en realizar sistemáticamente los procesos de puesta a punto del mismo, así tendremos las fases:
• Planificación. Estableceremos programas temporales y listas de verificación - protocolos de nuestra validación con criterios de aceptación/rechazo, necesidades de recursos, análisis de riesgos,... Esta planificación nos ahorrara mucho tiempo y esfuerzos en vano, hay que cuidarla.
• IQ - Cualificación de la instalación. Esta fase va asociada a la instalación por parte de nuestro proveedor del sistema e incluirá la calibración de los elementos de medición y control, la documentación, planos, instrucciones de trabajo, la cualificación y formación del equipo de validación...
• OQ - Cualificación operativa. Esta es la fase crucial de puesta a punto de nuestro proceso donde debe probarse su robustez y fiabilidad frente a casos peores. Es crítico aquí el diseño de experimentos para desafiar al proceso.
• PQ - Cualificación de prestaciones o funcional. En esta última fase se verá la repetitividad y reproducibilidad de nuestro proceso. La formación y cualificación precisa para su operación, instrucciones de trabajo definitivas, puestas en marcha, paradas, ... .
8. Inspección
La disposición de un lote puede determinarse inspeccionando cada unidad ("inspección al 100%") o inspeccionando una muestra o porción del lote.
9. Muestreo Aleatorio
Consideremos una población finita, de la que deseamos extraer una muestra. Cuando el proceso de extracción es tal que garantiza a cada uno de los elementos de la población la misma oportunidad de ser incluidos en dicha muestra, denominamos al proceso de selección muestreo aleatorio.
El muestreo aleatorio se puede plantear bajo dos puntos de vista:
• Sin reposición de los elementos;
• Con reposición
10. Muestreo Aleatorio Estratificado
Un muestreo aleatorio estratificado es aquel en el que se divide la población de N individuos, en k subpoblaciones o estratos, atendiendo a criterios que puedan ser importantes en el estudio, de tamaños respectivos N1, ..., Nk, y realizando en cada una de estas su poblaciones muestreos aleatorios simples de tamaño ni.

11. Muestreo Sistematico
En este caso se elige el primer individuo al azar y el resto viene condicionado por aquél. Este método es muy simple de aplicar en la práctica y tiene la ventaja de que no hace falta disponer de un marco de encuesta elaborado. Puede aplicarse en la mayoría de las situaciones, la única precaución que debe tenerse en cuenta es comprobar que la característica que estudiamos no tenga una periodicidad que coincida con la del muestreo (por ejemplo elegir un día de la semana para tomar muestras en un matadero, ya que muchos ganaderos suelen sacrificar un día determinado).

12. Auditoria de calidad
La auditoría de calidad es una herramienta de gestión empleada para verificar y evaluar las actividades relacionadas con la calidad en el seno de una organización. Su realización se inicia en una o varias de las situaciones siguientes:
Por solicitud de la Administración: la Administración puede someter a auditoría el sistema de gestión de la calidad de un centro de fabricación como una medida más dentro del proceso de homologación de un producto.
Por exigencia de un cliente: Un cliente puede exigir la auditoría del sistema de calidad del suministrador antes de iniciar o durante el desarrollo .
Por solicitud a una entidad de certificación: Cualquier organización puede solicitar la certificación de que su sistema de calidad es conforme al modelo adoptado y, en consecuencia, someterse a una auditoría.
Por exigencia del sistema de calidad propio: Según cual sea el modelo de gestión de la calidad adoptado, las auditorías internas se realizarán por personal interno con una regularidad periódica.
13. Prueba.
El efecto de proporcionar suficientes evidencias para persuadir al cliente o consumidor que el producto es de buena calidad
14. Control estadístico de procesos
El Control Estadístico de Procesos (C.E.P.), también conocido por sus siglas en inglés "SPC" es un conjunto de herramientas estadísticas que permiten recopilar, estudiar y analizar la información de procesos repetitivos para poder tomar decisiones encaminadas a la mejora de los mismos, es aplicable tanto a procesos productivos como de servicios siempre y cuando cumplan con dos condiciones: Que se mensurable (observable) y que sea repetitivo (Curso Teórico- Práctico CEP, 2004). El propósito fundamental de C.E.P. es identificar y eliminar las causas especiales de los problemas (variación) para llevar a los procesos nuevamente bajo control.
15. Defecto
Carencia de alguna cualidad propia de un producto o servicio.
16. No conformidad
Es un incumplimiento de los requisitos definidos (por el Sistema de Calidad y Medioambiente, por la ley, por las especificaciones del centro o de la Institución, etc.)
REFERENCIAS:
http://www.unap.cl/public/01%20Calidad%20Concepto%20y%20Definiciones.pdf
http://www.tecno-med.es/validacion_de_procesos.htm
http://www.estrucplan.com.ar/Producciones/Entrega.asp?identrega=438
http://www.bioestadistica.uma.es/libro/node88.htm
http://minnie.uab.es/~veteri/21216/TiposMuestreo1.pdf
http://sistemas.itlp.edu.mx/tutoriales/produccion1/tema2_7.htm
http://www.monografias.com/trabajos11/conge/conge.shtml
METROLOGIA
Todo el tiempo necesitamos medir, en el comercio, en la industria y en la vida diaria, debemos tomar decisiones a base de resultados de medición.
Metrología
La metrología (del griego μετρoν, medida y λoγoς, tratado) es la ciencia de la medida. Tiene por objetivo el estudio de los sistemas de medida en cualquier campo de la ciencia. También tiene como objetivo indirecto que se cumpla con la calidad.
La Metrología tiene dos características muy importantes como:
1. El resultado de la medición.
2. La incertidumbre de medida.
Los físicos y la industria utilizan una gran variedad de instrumentos para llevar a cabo sus mediciones. Desde objetos sencillos como reglas y cronómetros, hasta potentes microscopios, medidores de láser e incluso aceleradores de partículas.
La metrología permite asegurar la comparabilidad internacional de las mediciones y por tanto la intercambibilidad de los productos a nivel internacional.
Trazabilidad y Calibración
Es la propiedad de un resultado de medicion de estar relacionada a referencias establecidas llamadas patrones de medida.
Para saber que la balanza esta calibrada se pesan un conjunto de pesas patrones y se compara el valor indicado, verificando que coincida, este proceso es conocido como calibración. El patron primario de masa es una pesa de 1 kg de platino iridfiado mantenida en los laboratorios del Bureau Internacional de Pesasa y Medidas, en Francia.
Otros patrones primarios son conocidos a traves de experiencias fisicas, como en la temperatura cuyos valores 0 y 100 grados centigrados se registran cuando el agua se solidifica y se hierve, respectivamente. Otro patrones primarios de la temperatura son el mercurio y la plata; si calentamos un trozo de plata, se fundira hasta los 961 grados centigrados mientras que el mercurio se solidifica a los -39, obteniendose asi dos puntos fijos.
Repetibilidad
La repetibilidad (también conocida como coeficiente de correlación intraclase) es una medida estadística de la consistencia entre medidas repetidas de un mismo carácter en un mismo individuo. Generalmente se la denomina como ri y su valor se expresa como una proporción. Un valor de repetibilidad de uno indica que la medida es perfectamente consistente y repetible, y que el investigador no comete ningún error en la medición de ese carácter. Un valor de cero indica que las medidas repetidas obtenidas de ese carácter son tan distintas como si se hubieran tomado a partir de individuos distintos tomados al azar.
Reproducibilidad
se refiere a la capacidad que tenga una prueba o experimento de ser reproducido o replicado. El término está estrechamente relacionado con el concepto de testabilidad, y, dependiendo del campo científico en particular, puede requerir que la prueba o experimento sea falsable.
De forma particular, en metrologia se denomina reproducibilidad a la capacidad de un instrumento de dar el mismo resultado en mediciones diferentes realizadas en las mismas condiciones a lo largo de periodos dilatados de tiempo. Esta cualidad debe evaluarse a largo plazo. Ésta es la gran diferencia con precisión que debe, en cambio, ser evaluada a corto plazo.
Clasificación de Metrología
• Metrologia cientifica
• Metrologia Legal
• Metrologia Industrial
Vernier
El nonio o vernier es una segunda escala auxiliar que tienen algunos instrumentos de medición, que permite apreciar una medición con mayor precisión al complementar las divisiones de la regla o escala principal del instrumento de medida.
El sistema consiste en una regla sobre la que se han grabado una serie de divisiones según el sistema de unidades empleado, y una corredera o carro móvil, con un fiel o punto de medida, que se mueve a lo largo de la regla.

En una escala de medida, podemos apreciar hasta su unidad de división más pequeña, siendo esta la apreciación con la que se puede dar la medición; es fácil percatarse que entre una división y la siguiente hay más medidas, que unas veces está más próxima a la primera de ellas y otras a la siguiente.

Para poder apreciar distintos valores entre dos divisiones consecutivas, se ideó una segunda escala que se denomina nonio o vernier, grabada sobre la corredera y cuyo punto cero es el fiel de referencia. El nonio o vernier es esta segunda escala, no el instrumento de medida o el tipo de medida a realizar, tanto si es una medición lineal, angular, o de otra naturaleza, y sea cual fuere la unidad de medida. Esto es, si empleamos una regla para hacer una medida, solo podemos apreciar hasta la división más pequeña de esta regla; si además disponemos de una segunda escala, llamada nonio o vernier, podemos distinguir valores más pequeños.
El nonio o escala vernier toma un fragmento de la regla –que en el sistema decimal es un múltiplo de diez menos uno: 9, 19, etc.– y lo divide en un número más de divisiones: 10, 20.
En la figura se toman 9 divisiones de la regla y la dividen en diez partes iguales; es el caso más sencillo, de tal modo que cada una de estas divisiones sea de 0,9 unidades de la regla. Esto hace que si la división cero del nonio coincide con la división cero de la regla, la distancia entre la primera división de la regla y la primera del nonio sea de 0,1; que entre la segunda división de la regla y la segunda del nonio haya una diferencia de 0,2; y así, sucesivamente, de forma que entre la décima división de la regla y la décima del nonio haya 1,0, es decir: la décima división del nonio coincide con la novena de la regla, según se ha dicho en la forma de construcción del nonio. Esto hace que en todos los casos en los que el punto 0 del nonio coincide con una división de la regla el punto diez del nonio también lo hace.

Cuando la división uno del nonio coincide con una división de la regla, el fiel está separado 0,1 adelante. De modo general, el fiel indica el número entero de divisiones de la regla, y el nonio indica su posición entre dos divisiones sucesivas de la regla.
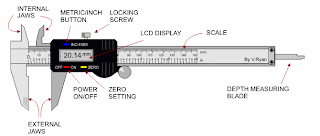
Micrómetro
Micrómetro: (del griego micros, pequeño, y metros, medición), también llamado Tornillo de Palmer, es un instrumento que sirve para medir con alta precisión (del orden de una micra, equivalente a 10 − 6 metros) las dimensiones de un objeto. Para ello cuenta con 2 puntas que se aproximan entre sí mediante un tornillo de rosca fina, el cual tiene grabado es su contorno una escala. La escala puede incluir un nonio. Frecuentemente el micrómetro también incluye una manera de limitar la torsión máxima del tornillo, dado que la rosca muy fina hace difícil notar fuerzas capaces de causar deterioro de la precisión del instrumento. El Micrómetro se clasifica de la siguiente manera:
• Micrómetro de exteriores: son instrumentos de medida capaces de medir el exterior de piezas en centésimas. Poseen contactos de metal duro rectificados y lapeados. Ejercen sobre la pieza a medir una presión media entre 5 y 10 N, poseen un freno para no dañar la pieza y el medidor si apretamos demasiado al medir.
• Micrómetro digital con precisión de 1 milésima: son exactamente iguales a los anteriores, pero tienen la particularidad de realizar mediciones de hasta 1 milésima de precisión y son digitales, a diferencia de los anteriores que son analógicos.
• Micrómetro exterior con contacto de platillos: de igual aspecto que los anteriores, pero posee unos platillos en sus contactos para mejor agarre y para la medición de dientes de coronas u hojas de sierra circulares.
• Micrómetro de exteriores de arco profundo: tiene la particularidad de que tiene su arco de mayor longitud que los anteriores, para poder realizar mediciones en placas o sitios de difícil acceso.
• Micrómetro de profundidades: éste tipo de micrómetros se parece mucho al calibre de profundidades, pero tiene la capacidad de realizar mediciones en centésimas.
• Micrómetro de interiores HOLTEST: tipo de micrómetro que mide interiores basándose en tres puntos de apoyo. En el estuche se contienen galgas para comprobar la exactitud de las mediciones.

Escalímetro
Un escalímetro (denominado algunas veces escala de arquitecto) es una regla especial cuya sección transversal tiene forma prismática con el objeto de contener diferentes escalas en la misma regla. Se emplea frecuentemente para medir en dibujos que contienen diversas escalas. En su borde contiene un rango con escalas calibradas y basta con girar sobre su eje longitudinal para ver la escala apropiada.
Los escalímetros planos contienen dos escalas que suelen ser:
1:1 / 1:100
1:5 / 1:50
1:20 / 1:200
1:1250 / 1:2500
En los escalímetros triangulares, los valores habituales son:
1:1 / 1:10
1:2 / 1:20
1:5 / 1:50
1:100 / 1:200
1:500 / 1:1000
1:1250 / 1:2500
Metrología
La metrología (del griego μετρoν, medida y λoγoς, tratado) es la ciencia de la medida. Tiene por objetivo el estudio de los sistemas de medida en cualquier campo de la ciencia. También tiene como objetivo indirecto que se cumpla con la calidad.
La Metrología tiene dos características muy importantes como:
1. El resultado de la medición.
2. La incertidumbre de medida.
Los físicos y la industria utilizan una gran variedad de instrumentos para llevar a cabo sus mediciones. Desde objetos sencillos como reglas y cronómetros, hasta potentes microscopios, medidores de láser e incluso aceleradores de partículas.
La metrología permite asegurar la comparabilidad internacional de las mediciones y por tanto la intercambibilidad de los productos a nivel internacional.
Trazabilidad y Calibración
Es la propiedad de un resultado de medicion de estar relacionada a referencias establecidas llamadas patrones de medida.
Para saber que la balanza esta calibrada se pesan un conjunto de pesas patrones y se compara el valor indicado, verificando que coincida, este proceso es conocido como calibración. El patron primario de masa es una pesa de 1 kg de platino iridfiado mantenida en los laboratorios del Bureau Internacional de Pesasa y Medidas, en Francia.
Otros patrones primarios son conocidos a traves de experiencias fisicas, como en la temperatura cuyos valores 0 y 100 grados centigrados se registran cuando el agua se solidifica y se hierve, respectivamente. Otro patrones primarios de la temperatura son el mercurio y la plata; si calentamos un trozo de plata, se fundira hasta los 961 grados centigrados mientras que el mercurio se solidifica a los -39, obteniendose asi dos puntos fijos.
Repetibilidad
La repetibilidad (también conocida como coeficiente de correlación intraclase) es una medida estadística de la consistencia entre medidas repetidas de un mismo carácter en un mismo individuo. Generalmente se la denomina como ri y su valor se expresa como una proporción. Un valor de repetibilidad de uno indica que la medida es perfectamente consistente y repetible, y que el investigador no comete ningún error en la medición de ese carácter. Un valor de cero indica que las medidas repetidas obtenidas de ese carácter son tan distintas como si se hubieran tomado a partir de individuos distintos tomados al azar.
Reproducibilidad
se refiere a la capacidad que tenga una prueba o experimento de ser reproducido o replicado. El término está estrechamente relacionado con el concepto de testabilidad, y, dependiendo del campo científico en particular, puede requerir que la prueba o experimento sea falsable.
De forma particular, en metrologia se denomina reproducibilidad a la capacidad de un instrumento de dar el mismo resultado en mediciones diferentes realizadas en las mismas condiciones a lo largo de periodos dilatados de tiempo. Esta cualidad debe evaluarse a largo plazo. Ésta es la gran diferencia con precisión que debe, en cambio, ser evaluada a corto plazo.
Clasificación de Metrología
• Metrologia cientifica
• Metrologia Legal
• Metrologia Industrial
Vernier
El nonio o vernier es una segunda escala auxiliar que tienen algunos instrumentos de medición, que permite apreciar una medición con mayor precisión al complementar las divisiones de la regla o escala principal del instrumento de medida.
El sistema consiste en una regla sobre la que se han grabado una serie de divisiones según el sistema de unidades empleado, y una corredera o carro móvil, con un fiel o punto de medida, que se mueve a lo largo de la regla.

En una escala de medida, podemos apreciar hasta su unidad de división más pequeña, siendo esta la apreciación con la que se puede dar la medición; es fácil percatarse que entre una división y la siguiente hay más medidas, que unas veces está más próxima a la primera de ellas y otras a la siguiente.

Para poder apreciar distintos valores entre dos divisiones consecutivas, se ideó una segunda escala que se denomina nonio o vernier, grabada sobre la corredera y cuyo punto cero es el fiel de referencia. El nonio o vernier es esta segunda escala, no el instrumento de medida o el tipo de medida a realizar, tanto si es una medición lineal, angular, o de otra naturaleza, y sea cual fuere la unidad de medida. Esto es, si empleamos una regla para hacer una medida, solo podemos apreciar hasta la división más pequeña de esta regla; si además disponemos de una segunda escala, llamada nonio o vernier, podemos distinguir valores más pequeños.
El nonio o escala vernier toma un fragmento de la regla –que en el sistema decimal es un múltiplo de diez menos uno: 9, 19, etc.– y lo divide en un número más de divisiones: 10, 20.
En la figura se toman 9 divisiones de la regla y la dividen en diez partes iguales; es el caso más sencillo, de tal modo que cada una de estas divisiones sea de 0,9 unidades de la regla. Esto hace que si la división cero del nonio coincide con la división cero de la regla, la distancia entre la primera división de la regla y la primera del nonio sea de 0,1; que entre la segunda división de la regla y la segunda del nonio haya una diferencia de 0,2; y así, sucesivamente, de forma que entre la décima división de la regla y la décima del nonio haya 1,0, es decir: la décima división del nonio coincide con la novena de la regla, según se ha dicho en la forma de construcción del nonio. Esto hace que en todos los casos en los que el punto 0 del nonio coincide con una división de la regla el punto diez del nonio también lo hace.

Cuando la división uno del nonio coincide con una división de la regla, el fiel está separado 0,1 adelante. De modo general, el fiel indica el número entero de divisiones de la regla, y el nonio indica su posición entre dos divisiones sucesivas de la regla.
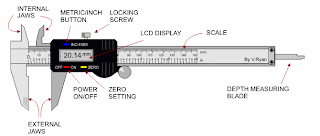
Micrómetro
Micrómetro: (del griego micros, pequeño, y metros, medición), también llamado Tornillo de Palmer, es un instrumento que sirve para medir con alta precisión (del orden de una micra, equivalente a 10 − 6 metros) las dimensiones de un objeto. Para ello cuenta con 2 puntas que se aproximan entre sí mediante un tornillo de rosca fina, el cual tiene grabado es su contorno una escala. La escala puede incluir un nonio. Frecuentemente el micrómetro también incluye una manera de limitar la torsión máxima del tornillo, dado que la rosca muy fina hace difícil notar fuerzas capaces de causar deterioro de la precisión del instrumento. El Micrómetro se clasifica de la siguiente manera:
• Micrómetro de exteriores: son instrumentos de medida capaces de medir el exterior de piezas en centésimas. Poseen contactos de metal duro rectificados y lapeados. Ejercen sobre la pieza a medir una presión media entre 5 y 10 N, poseen un freno para no dañar la pieza y el medidor si apretamos demasiado al medir.
• Micrómetro digital con precisión de 1 milésima: son exactamente iguales a los anteriores, pero tienen la particularidad de realizar mediciones de hasta 1 milésima de precisión y son digitales, a diferencia de los anteriores que son analógicos.
• Micrómetro exterior con contacto de platillos: de igual aspecto que los anteriores, pero posee unos platillos en sus contactos para mejor agarre y para la medición de dientes de coronas u hojas de sierra circulares.
• Micrómetro de exteriores de arco profundo: tiene la particularidad de que tiene su arco de mayor longitud que los anteriores, para poder realizar mediciones en placas o sitios de difícil acceso.
• Micrómetro de profundidades: éste tipo de micrómetros se parece mucho al calibre de profundidades, pero tiene la capacidad de realizar mediciones en centésimas.
• Micrómetro de interiores HOLTEST: tipo de micrómetro que mide interiores basándose en tres puntos de apoyo. En el estuche se contienen galgas para comprobar la exactitud de las mediciones.

Escalímetro
Un escalímetro (denominado algunas veces escala de arquitecto) es una regla especial cuya sección transversal tiene forma prismática con el objeto de contener diferentes escalas en la misma regla. Se emplea frecuentemente para medir en dibujos que contienen diversas escalas. En su borde contiene un rango con escalas calibradas y basta con girar sobre su eje longitudinal para ver la escala apropiada.
Los escalímetros planos contienen dos escalas que suelen ser:
1:1 / 1:100
1:5 / 1:50
1:20 / 1:200
1:1250 / 1:2500
En los escalímetros triangulares, los valores habituales son:
1:1 / 1:10
1:2 / 1:20
1:5 / 1:50
1:100 / 1:200
1:500 / 1:1000
1:1250 / 1:2500

UTILIZACION DE LOS METODOS ESTADISTICOS
UTILIZACION DE LOS METODOS ESTADISTICOS
Los Métodos estadísticos
En 1949 se empezaron a utilizar los métodos estadísticos en Japón, los cuales se dividen en método estadístico elemental, el método estadístico intermedio y el método estadístico avanzado.
1. Método estadístico Elemental
• Cuadro de Pareto: El principio de pocos vitales, muchos triviales
• Diagrama de Causa y Efecto
• Estratificación
• Hoja de Verificación
• Histograma
• Diagrama de dispersión
• Graficas y cuadros de control
Estos métodos fueron bautizados como las siete herramientas indispensables para el control de la calidad, llamadas así análogamente por las siete herramientas que utilizo el guerrero Benkey en el siglo doce. Según Kauro Ishikawa el 95% de los problemas de la empresa se resolvían mediante estas herramientas.
2. Método estadístico Intermedio
• Teoría del muestreo
• Inspección estadística por muestreo
• Diversos métodos de realizar estimaciones y pruebas estadísticas
• Métodos de utilización de pruebas sensoriales
• Métodos de diseñar experimentos
Los métodos estadísticos intermedios enseñan a los ingenieros y a los miembros de promoción del control de calidad (CC). Ha tenido mucho éxito en Japón
3. Método estadístico avanzado
• Métodos avanzados de diseñar experimentos
• Análisis de multivariables
• Diversos métodos de investigación de operaciones
Han sido la base de una alta tecnología y ha levantado sorprendentemente la industria japonesa.
Problemas Relativos a la utilización de métodos estadísticos en las industrias
A pesar de la implementación de los métodos estadísticos y la adaptación del lema “Hablamos con datos” (utilizamos métodos estadísticos), todavía quedan serios problemas por resolver
1. Datos falsos y datos que no concuerdan con los hechos
Existen dos casos en que los datos y los hechos no concuerdan, el primer caso se da cuando los datos se adulteran, esto ocurre cuando le empresa esta muy centralizada y la gerencia carece de la dispersión en estadística, y en el segundo caso, simplemente hay ignorancia de los métodos estadísticos
2. Métodos deficientes de reunir datos
En la industria minera japonesa, los métodos de muestreo, división medición y análisis no eran los adecuados así que Kauro Ishikawa decidió dividir el estudio de la muestra minera en subgrupos sobre mineral de fierro, metales no ferrosos, carbón , coke, mineral de azufre, sales industriales e instrumentos de muestreo llegando al punto en que las normas japonesas de la minería fueran aceptadas por la ISO, sin embargo, todavía queda determinar la solución de los problemas ambientales, es decir, cuantas partes por millón de ciertas sustancias como el mercurio serán aceptadas y que limites se establecerán.
3. Transcripción errada de los datos y cálculos equivocados
Los errores debidos a equivocaciones elementales son muy frecuentes. Por fortuna, los expertos en estadística pueden descubrirlos con facilidad.
4. Valores Anormales
Los datos relativos a una sociedad en general y a la industria suelen ser impuros porque contienen valores anómalos. Hay ciertos casos en que los datos contienen valores anormales que realmente existen, lo que genera un dilema al deber aceptar los valores o no.
5. Falta de Fortaleza
Las herramientas y los métodos estadísticos sofisticados carecen de fortaleza y tienen una aplicación limitada y pueden ser inapropiados para ciertos casos. En cambio las siete herramientas básicas son fuertes y se pueden usar en cualquier situación.
6. Método de aplicación equivocado
Los inexpertos suelen cometer errores al utilizar métodos estadísticos o analíticos. Estos se debe a su falta de clara comprensión de las teorías estadísticas y de los modelos estructurales, por lo que, según Ishikawa, deben ser vigilados por personas expertas.
Análisis estadísticos
En las industrias se emplean principalmente dos métodos estadísticos para el análisis, el análisis de calidad y el de procesos. El análisis de calidad es el que con ayuda de datos y métodos estadísticos determina las características de calidad reales y las sustitutas. Mientras que el análisis de procesos aclara la relación entre los factores casuales y los efectos tales como calidad, costo productividad, etc., cuando se esta efectuando el control de procesos, este control busca descubrir las causas que impiden el funcionamiento del proceso manufacturero y así encontrar una tecnología para el control preventivo.
Uno de los puntos fuertes de las industrias japonesas ha sido su éxito en el control dinámico computarizado mediante el manejo eficaz del análisis de procesos. En efecto, su índice de control es menor de uno por millón en su control de procesos. Mediante el análisis pueden estudiar la capacidad estadística de los procesos.
Control Estadístico
En diversas medidas de control tales como el círculo PHVA, se cuestiona como verificar los resultados, a pesar de que los resultados sean los correctos.
Es necesario recordar que las causas que pueden afectar los procesos fabriles y cualquier otro tipo de trabajo son ilimitadas; por eso los efectos serán dispersos. Por tanto al verificar se debe guiar por el concepto de distribución. Los cuadros de control que suelen utilizarse hoy en el Japón son el cuadro x-R, el cuadro x-R, el cuadro p, el cuadro pn, el cuadro c y el cuadro u. Muchos gerentes y trabajadores de diversas plantas los han aplicado con muy buenos resultados.
Métodos estadísticos y progreso tecnológico
Para utilizar los métodos estadísticos mas avanzados primero se deben dominar las siete herramientas básicas. Por los métodos estadísticos se mejoro el nivel de calidad, se aumento la confiabilidad y se bajaron los costos en Japón. Esto ha dado como resultado la mejora de la tecnología.
Es preciso utilizar toda la tecnología disponible para mejorar la calidad y la eficiencia. Después de la segunda guerra mundial Japón importo mucha tecnología del occidente, hoy tiene la capacidad de exportarla; esto se debe a que gran parte de la introducción del control de calidad estadístico y al empleo del análisis estadístico, del análisis de procesos, y del análisis de calidad.
Aun existen muchos problemas y siempre hay campo para mejorar, pero si los métodos estadísticos logran penetrar en áreas distintas de la industria, la nación mejorará.
Los Métodos estadísticos
En 1949 se empezaron a utilizar los métodos estadísticos en Japón, los cuales se dividen en método estadístico elemental, el método estadístico intermedio y el método estadístico avanzado.
1. Método estadístico Elemental
• Cuadro de Pareto: El principio de pocos vitales, muchos triviales
• Diagrama de Causa y Efecto
• Estratificación
• Hoja de Verificación
• Histograma
• Diagrama de dispersión
• Graficas y cuadros de control
Estos métodos fueron bautizados como las siete herramientas indispensables para el control de la calidad, llamadas así análogamente por las siete herramientas que utilizo el guerrero Benkey en el siglo doce. Según Kauro Ishikawa el 95% de los problemas de la empresa se resolvían mediante estas herramientas.
2. Método estadístico Intermedio
• Teoría del muestreo
• Inspección estadística por muestreo
• Diversos métodos de realizar estimaciones y pruebas estadísticas
• Métodos de utilización de pruebas sensoriales
• Métodos de diseñar experimentos
Los métodos estadísticos intermedios enseñan a los ingenieros y a los miembros de promoción del control de calidad (CC). Ha tenido mucho éxito en Japón
3. Método estadístico avanzado
• Métodos avanzados de diseñar experimentos
• Análisis de multivariables
• Diversos métodos de investigación de operaciones
Han sido la base de una alta tecnología y ha levantado sorprendentemente la industria japonesa.
Problemas Relativos a la utilización de métodos estadísticos en las industrias
A pesar de la implementación de los métodos estadísticos y la adaptación del lema “Hablamos con datos” (utilizamos métodos estadísticos), todavía quedan serios problemas por resolver
1. Datos falsos y datos que no concuerdan con los hechos
Existen dos casos en que los datos y los hechos no concuerdan, el primer caso se da cuando los datos se adulteran, esto ocurre cuando le empresa esta muy centralizada y la gerencia carece de la dispersión en estadística, y en el segundo caso, simplemente hay ignorancia de los métodos estadísticos
2. Métodos deficientes de reunir datos
En la industria minera japonesa, los métodos de muestreo, división medición y análisis no eran los adecuados así que Kauro Ishikawa decidió dividir el estudio de la muestra minera en subgrupos sobre mineral de fierro, metales no ferrosos, carbón , coke, mineral de azufre, sales industriales e instrumentos de muestreo llegando al punto en que las normas japonesas de la minería fueran aceptadas por la ISO, sin embargo, todavía queda determinar la solución de los problemas ambientales, es decir, cuantas partes por millón de ciertas sustancias como el mercurio serán aceptadas y que limites se establecerán.
3. Transcripción errada de los datos y cálculos equivocados
Los errores debidos a equivocaciones elementales son muy frecuentes. Por fortuna, los expertos en estadística pueden descubrirlos con facilidad.
4. Valores Anormales
Los datos relativos a una sociedad en general y a la industria suelen ser impuros porque contienen valores anómalos. Hay ciertos casos en que los datos contienen valores anormales que realmente existen, lo que genera un dilema al deber aceptar los valores o no.
5. Falta de Fortaleza
Las herramientas y los métodos estadísticos sofisticados carecen de fortaleza y tienen una aplicación limitada y pueden ser inapropiados para ciertos casos. En cambio las siete herramientas básicas son fuertes y se pueden usar en cualquier situación.
6. Método de aplicación equivocado
Los inexpertos suelen cometer errores al utilizar métodos estadísticos o analíticos. Estos se debe a su falta de clara comprensión de las teorías estadísticas y de los modelos estructurales, por lo que, según Ishikawa, deben ser vigilados por personas expertas.
Análisis estadísticos
En las industrias se emplean principalmente dos métodos estadísticos para el análisis, el análisis de calidad y el de procesos. El análisis de calidad es el que con ayuda de datos y métodos estadísticos determina las características de calidad reales y las sustitutas. Mientras que el análisis de procesos aclara la relación entre los factores casuales y los efectos tales como calidad, costo productividad, etc., cuando se esta efectuando el control de procesos, este control busca descubrir las causas que impiden el funcionamiento del proceso manufacturero y así encontrar una tecnología para el control preventivo.
Uno de los puntos fuertes de las industrias japonesas ha sido su éxito en el control dinámico computarizado mediante el manejo eficaz del análisis de procesos. En efecto, su índice de control es menor de uno por millón en su control de procesos. Mediante el análisis pueden estudiar la capacidad estadística de los procesos.
Control Estadístico
En diversas medidas de control tales como el círculo PHVA, se cuestiona como verificar los resultados, a pesar de que los resultados sean los correctos.
Es necesario recordar que las causas que pueden afectar los procesos fabriles y cualquier otro tipo de trabajo son ilimitadas; por eso los efectos serán dispersos. Por tanto al verificar se debe guiar por el concepto de distribución. Los cuadros de control que suelen utilizarse hoy en el Japón son el cuadro x-R, el cuadro x-R, el cuadro p, el cuadro pn, el cuadro c y el cuadro u. Muchos gerentes y trabajadores de diversas plantas los han aplicado con muy buenos resultados.
Métodos estadísticos y progreso tecnológico
Para utilizar los métodos estadísticos mas avanzados primero se deben dominar las siete herramientas básicas. Por los métodos estadísticos se mejoro el nivel de calidad, se aumento la confiabilidad y se bajaron los costos en Japón. Esto ha dado como resultado la mejora de la tecnología.
Es preciso utilizar toda la tecnología disponible para mejorar la calidad y la eficiencia. Después de la segunda guerra mundial Japón importo mucha tecnología del occidente, hoy tiene la capacidad de exportarla; esto se debe a que gran parte de la introducción del control de calidad estadístico y al empleo del análisis estadístico, del análisis de procesos, y del análisis de calidad.
Aun existen muchos problemas y siempre hay campo para mejorar, pero si los métodos estadísticos logran penetrar en áreas distintas de la industria, la nación mejorará.
GURUS DE LA CALIDAD
GURÚS DE LA CALIDAD
1. William Edwards Deming
Impulsor del desarrollo en calidad de Japón, fue invitado en 1950 por la Unión de Científicos e Ingenieros del Japón ( JUSE ), logrando que implementaran el Control Total de Calidad usando el ciclo PHVA (Planear, Hacer, Verificar y Actuar) de Shewhart y el Control Estadístico de Procesos.

Se le considera el "Padre" de la Tercera Revolución Industrial o La Revolución de la Calidad, con sus famosos 14 puntos.
LOS 14 PUNTOS
1. CONSTANCIA
El propósito es mejorar constantemente los productos y servicios de la empresa, teniendo como objetivo la consecución de la competitividad permaneciendo en el mercado para proporcionar empleo por medio de la innovación, la investigación, el mejoramiento continuo y el mantenimiento adecuado.
2. NUEVA FILOSOFÍA
Se trata de adoptar una nueva filosofía de empresa ya que estamos viviendo una nueva era económica (mucho más ahora) en la que los gerentes deben tomar conciencia de sus responsabilidades y afrontar la cuota de liderazgo que les cabe para lograr el cambio
3. LA INSPECCIÓN
Se debe dejar de depender de la inspección masiva para alcanzar la calidad, hay que eliminar la inspección en masa a través de la integración del concepto de calidad en todo el proceso de producción, lo cual aminora costos y permite aumentar calidad.
4. LAS COMPRAS
Hay que eliminar la práctica de comprar basándose exclusivamente en el precio, ya que los departamentos de compras tienden a elegir al proveedor con los precios más bajos. En su lugar, se deben concentrar esfuerzos en minimizar los costos totales, creando relaciones sólidas y duraderas con un solo proveedor para cada materia prima, basándose en la fidelidad y la confianza.
5. MEJORAMIENTO CONTINUO
La búsqueda por mejorar debe ser continua, no momentánea ni estática, se deben mejorar los procesos productivos, el servicio y la planificación, además la administración debe tender a la minimización de costos a través de la reducción de pérdidas y mermas y productos defectuosos.
6. ENTRENAMIENTO
Se debe instituir el entrenamiento y la capacitación de los trabajadores como una de las tareas del diario acontecer, con esto no sólo se consiguen mejores empleados sino mayores resultados en cuanto a calidad y costos.
7. LIDERAZGO
Las organizaciones deben adoptar e instituir el liderazgo, de manera que la labor de los supervisores o jefes no se limite a dar órdenes o impartir castigos, sino que más bien se convierta en un orientador que le ayude a la gente a hacer mejor su trabajo y que identifique quiénes son las personas que necesitan mayor ayuda para hacerlo.
8. EL MIEDO
Las firmas deben desterrar el temor y el miedo de todos sus niveles, hay que generar confianza entre la gente de manera que no sientan temor de opinar o preguntar, esto permite mayor efectividad en el trabajo y permite que las personas se esfuercen porque quieren que la empresa alcance el éxito.
9. BARRERAS
Romper las barreras que existan entre los diferentes departamentos y su gente, no crear competencias que las hagan chocar sino más bien generar la visión de largo plazo que les permita a todos trabajar por conseguir los mismo objetivos, permitiendo así la colaboración y la detección temprana de fallos.
10. SLOGANS
Hay que borrar los slogans o las frases preestablecidas, estos no sirven y lo que causan es relaciones adversas que redundan en pérdidas de competitividad y calidad.
11. CUOTAS
Deben eliminarse las cuotas numéricas, tanto para trabajadores como para gerentes. Las cuotas sólo toman en cuenta los números, no los procesos, los métodos o la calidad y por lo general se constituyen en garantía de baja calidad y altos costos. Las cuotas se deben sustituir con liderazgo, eliminando el concepto de gerencia por objetivos.
12. LOGROS PERSONALES
Hay que derribar las barreras que le quitan a las personas el orgullo que les produce su trabajo, eliminando los sistemas de comparación o de méritos, estos sistemas sólo acarrean nerviosismo y disputas internas.
13. CAPACITACIÓN
Se debe establecer un programa interno de educación y automejoramiento para cada quien, hay que permitir la participación de la gente en la elección de las áreas de desarrollo
14.TRANSFORMACIÓN
Todos, absolutamente todos los miembros de la organización deben esforzarse por alcanzar la transformación en cuanto a calidad, procesos, productos y servicios, la transformación es el trabajo de todos, pero eso si, hay que basarse en un equipo que reúna condiciones suficientes de capacidad y liderazgo.
2. Joseph M. Juran
Afirma que la Alta Administración es la responsable del cambio, abogando por crear el cambio cuando el proceso necesita mejorarse y por prevenir el cambio cuando los problemas son esporádicos. Logró desarrollar la técnica de los Costos de Calidad, elaborando un Manual de Calidad, en donde existe un fuerte contenido administrativo enfocado a la planificación, organización y responsabilidad.
En 1954 fue invitado por el JUSE para dar conferencias en Japón, por lo que junto con Deming e Ishikawa se les considera los principales promotores del éxito de Japón. Su aportación más importante es la llamada "Trilogía de Juran", que son los tres procesos necesarios para la administración de la calidad:
1. Planificación de la calidad.
Es la actividad de desarrollo de los productos y procesos requeridos para satisfacer las necesidades de los clientes
a) Determinar quiénes son los clientes.
b) Determinar las necesidades de los clientes.
c) Desarrollar las características del producto que responden a las necesidades de los clientes.
d) Desarrollar los procesos que sean capaces de producir aquellas características del producto.
e) Transferir los planes resultantes a las fuerzas operativas
2. Control de calidad.
a) Evaluar el comportamiento real de la calidad.
b) Comparar el comportamiento real con los objetivos de calidad.
c) Actuar sobre las diferencias.
2. Mejora de la calidad.
Este proceso es el medio de elevar la calidad a niveles sin precedente.
a) Establecer la infraestructura necesaria para conseguir una mejora de la calidad anualmente.
b) Identificar las necesidades concretas para mejorar (los proyectos de mejora).
c) Establecer un equipo de personas para cada proyecto con una responsabilidad clara de llevar el proyecto a buen fin.
d) Proporcionar los recursos, la motivación y la formación necesaria para que los equipos:
– Diagnostiquen las causas.
– Fomenten el establecimiento de un remedio.
– Establezcan los controles para mantener los beneficios.
Igualmente, otra aportación de Juran es la llamada "Espiral del progreso de la calidad".

3.Kaoru Ishikawa
La mayor contribución de Ishikawa fue simplificar los métodos estadísticos utilizados para control de calidad en la industria a nivel general. A nivel técnico su trabajo enfatizó la buena recolección de datos y elaborar una buena presentación, también utilizó los diagramas de Pareto para priorizar las mejorías de calidad, también los diagramas de Ishikawa, diagramas de Pescado o diagramas de Causa y Efecto.
Establece que los diagramas de causa y efecto como herramienta para asistir los grupos de trabajo que se dedican a mejorar la calidad. Cree que la comunicación abierta es fundamental para desarrollar dichos diagramas. Estos diagramas resultan útiles para encontrar, ordenar y documentar las causas de la variación de calidad en producción.

Otro trabajo de Ishikawa es el control de calidad a nivel empresarial (CWQC). Este enfatiza que la calidad debe observarse y lograrse no solo a nivel de producto sino también en el área de ventas, calidad de administración, la compañía en sí y la vida personal. Los resultados de este enfoque son:
1. La calidad del producto es mejorada y uniforme, se reducen los defectos.
2. Se logra una mayor confiabilidad hacia la empresa.
3. Se reduce el costo.
4. Se incrementa la cantidad de producción, lo cual facilita la realización y cumplimiento de horarios y metas.
5. El trabajo de desperdicio y el retrabajar se reducen.
6. Se establece y se mejora una técnica.
7. Los gastos de inspección y pruebas se reducen.
8. Se racionalizan los contratos entre vendedor y cliente
9. Se amplia el Mercado de operaciones.
10. Se mejoran las relaciones entre departamentos.
11. Se reducen la información y reportes falsos.
12. Las discusiones son más libres y democráticas.
13. Las juntas son mas eficientes.
14. Las reparaciones e instalación de equipo son más realistas
15. Se mejoran las relaciones humanas.
La filosofía de Ishikawa se resume en:
• La calidad empieza y termina con educación.
• El primer paso en calidad es conocer las necesidades de los clientes.
• El estado ideal del Control de Calidad es cuando la inspección ya no es necesaria.
• Es necesario remover las raíces y no los síntomas de los problemas.
• El control de calidad es responsabilidad de toda la organización.
• No se deben confundir los medios con los objetivos.
• Se debe poner en primer lugar la calidad, los beneficios financieros vendrán como consecuencia.
• La Mercadotecnia es la entrada y éxito de la calidad
• La Alta Administración no debe mostrar resentimientos cuando los hechos son presentados por sus subordinados.
• El 95% de los problemas de la compañía pueden ser resueltos con las 7 herramientas para el control de la calidad.
• Los datos sin dispersión son falsos.
Practicar el Control de Calidad es desarrollar, diseñar, manufacturar y mantener un producto de calidad que sea el más económico, el más útil y siempre satisfactorio para el consumidor.
4. Philip Crosby
Crosby es un pensador que desarrolló el tema de la calidad en años muy recientes. Sus estudios se enfocan en prevenir y evitar la inspección se busca que el cliente salga satisfecho al cumplir ciertos requisitos desde la primera vez y todas las veces que el cliente realice transacciones con una empresa.
En 1979 se crea la fundación Philip Associates II Inc. la cual se le considera una firma líder en consultorías acerca de la calidad. Se basan en la creencia de que la calidad puede ser medida y utilizada par mejorar los resultados empresariales, por esto se le considera una herramienta muy útil para competir en un Mercado cada vez más globalizado.
Crosby tiene el pensamiento que la calidad es gratis, es suplir los requerimientos de un cliente, al lograr cumplir con estos logramos Cero Defectos. En las empresas donde no se contempla la calidad los desperdicios y esfuerzos de más pueden llegar del 20% al 40% de la producción. Para lograr Cero Defectos promueve catorce pasos los cuales son:
1. Compromiso de la dirección
2. Equipo para la mejora de la calidad
3. Medición del nivel de calidad
4. Evaluación del costo de la calidad
5. Conciencia de la calidad
6. Sistema de acciones correctivas
7. Establecer comité del Programa Cero Defectos
8. Entrenamiento en supervisión
9. Establecer el día "Cero defectos"
10. Fijar metas
11. Remover causas de errores
12. Dar reconocimiento
13. Formar consejos de calidad
14. Repetir todo de nuevo
1. William Edwards Deming
Impulsor del desarrollo en calidad de Japón, fue invitado en 1950 por la Unión de Científicos e Ingenieros del Japón ( JUSE ), logrando que implementaran el Control Total de Calidad usando el ciclo PHVA (Planear, Hacer, Verificar y Actuar) de Shewhart y el Control Estadístico de Procesos.

Se le considera el "Padre" de la Tercera Revolución Industrial o La Revolución de la Calidad, con sus famosos 14 puntos.
LOS 14 PUNTOS
1. CONSTANCIA
El propósito es mejorar constantemente los productos y servicios de la empresa, teniendo como objetivo la consecución de la competitividad permaneciendo en el mercado para proporcionar empleo por medio de la innovación, la investigación, el mejoramiento continuo y el mantenimiento adecuado.
2. NUEVA FILOSOFÍA
Se trata de adoptar una nueva filosofía de empresa ya que estamos viviendo una nueva era económica (mucho más ahora) en la que los gerentes deben tomar conciencia de sus responsabilidades y afrontar la cuota de liderazgo que les cabe para lograr el cambio
3. LA INSPECCIÓN
Se debe dejar de depender de la inspección masiva para alcanzar la calidad, hay que eliminar la inspección en masa a través de la integración del concepto de calidad en todo el proceso de producción, lo cual aminora costos y permite aumentar calidad.
4. LAS COMPRAS
Hay que eliminar la práctica de comprar basándose exclusivamente en el precio, ya que los departamentos de compras tienden a elegir al proveedor con los precios más bajos. En su lugar, se deben concentrar esfuerzos en minimizar los costos totales, creando relaciones sólidas y duraderas con un solo proveedor para cada materia prima, basándose en la fidelidad y la confianza.
5. MEJORAMIENTO CONTINUO
La búsqueda por mejorar debe ser continua, no momentánea ni estática, se deben mejorar los procesos productivos, el servicio y la planificación, además la administración debe tender a la minimización de costos a través de la reducción de pérdidas y mermas y productos defectuosos.
6. ENTRENAMIENTO
Se debe instituir el entrenamiento y la capacitación de los trabajadores como una de las tareas del diario acontecer, con esto no sólo se consiguen mejores empleados sino mayores resultados en cuanto a calidad y costos.
7. LIDERAZGO
Las organizaciones deben adoptar e instituir el liderazgo, de manera que la labor de los supervisores o jefes no se limite a dar órdenes o impartir castigos, sino que más bien se convierta en un orientador que le ayude a la gente a hacer mejor su trabajo y que identifique quiénes son las personas que necesitan mayor ayuda para hacerlo.
8. EL MIEDO
Las firmas deben desterrar el temor y el miedo de todos sus niveles, hay que generar confianza entre la gente de manera que no sientan temor de opinar o preguntar, esto permite mayor efectividad en el trabajo y permite que las personas se esfuercen porque quieren que la empresa alcance el éxito.
9. BARRERAS
Romper las barreras que existan entre los diferentes departamentos y su gente, no crear competencias que las hagan chocar sino más bien generar la visión de largo plazo que les permita a todos trabajar por conseguir los mismo objetivos, permitiendo así la colaboración y la detección temprana de fallos.
10. SLOGANS
Hay que borrar los slogans o las frases preestablecidas, estos no sirven y lo que causan es relaciones adversas que redundan en pérdidas de competitividad y calidad.
11. CUOTAS
Deben eliminarse las cuotas numéricas, tanto para trabajadores como para gerentes. Las cuotas sólo toman en cuenta los números, no los procesos, los métodos o la calidad y por lo general se constituyen en garantía de baja calidad y altos costos. Las cuotas se deben sustituir con liderazgo, eliminando el concepto de gerencia por objetivos.
12. LOGROS PERSONALES
Hay que derribar las barreras que le quitan a las personas el orgullo que les produce su trabajo, eliminando los sistemas de comparación o de méritos, estos sistemas sólo acarrean nerviosismo y disputas internas.
13. CAPACITACIÓN
Se debe establecer un programa interno de educación y automejoramiento para cada quien, hay que permitir la participación de la gente en la elección de las áreas de desarrollo
14.TRANSFORMACIÓN
Todos, absolutamente todos los miembros de la organización deben esforzarse por alcanzar la transformación en cuanto a calidad, procesos, productos y servicios, la transformación es el trabajo de todos, pero eso si, hay que basarse en un equipo que reúna condiciones suficientes de capacidad y liderazgo.
2. Joseph M. Juran
Afirma que la Alta Administración es la responsable del cambio, abogando por crear el cambio cuando el proceso necesita mejorarse y por prevenir el cambio cuando los problemas son esporádicos. Logró desarrollar la técnica de los Costos de Calidad, elaborando un Manual de Calidad, en donde existe un fuerte contenido administrativo enfocado a la planificación, organización y responsabilidad.
En 1954 fue invitado por el JUSE para dar conferencias en Japón, por lo que junto con Deming e Ishikawa se les considera los principales promotores del éxito de Japón. Su aportación más importante es la llamada "Trilogía de Juran", que son los tres procesos necesarios para la administración de la calidad:
1. Planificación de la calidad.
Es la actividad de desarrollo de los productos y procesos requeridos para satisfacer las necesidades de los clientes
a) Determinar quiénes son los clientes.
b) Determinar las necesidades de los clientes.
c) Desarrollar las características del producto que responden a las necesidades de los clientes.
d) Desarrollar los procesos que sean capaces de producir aquellas características del producto.
e) Transferir los planes resultantes a las fuerzas operativas
2. Control de calidad.
a) Evaluar el comportamiento real de la calidad.
b) Comparar el comportamiento real con los objetivos de calidad.
c) Actuar sobre las diferencias.
2. Mejora de la calidad.
Este proceso es el medio de elevar la calidad a niveles sin precedente.
a) Establecer la infraestructura necesaria para conseguir una mejora de la calidad anualmente.
b) Identificar las necesidades concretas para mejorar (los proyectos de mejora).
c) Establecer un equipo de personas para cada proyecto con una responsabilidad clara de llevar el proyecto a buen fin.
d) Proporcionar los recursos, la motivación y la formación necesaria para que los equipos:
– Diagnostiquen las causas.
– Fomenten el establecimiento de un remedio.
– Establezcan los controles para mantener los beneficios.
Igualmente, otra aportación de Juran es la llamada "Espiral del progreso de la calidad".

3.Kaoru Ishikawa
La mayor contribución de Ishikawa fue simplificar los métodos estadísticos utilizados para control de calidad en la industria a nivel general. A nivel técnico su trabajo enfatizó la buena recolección de datos y elaborar una buena presentación, también utilizó los diagramas de Pareto para priorizar las mejorías de calidad, también los diagramas de Ishikawa, diagramas de Pescado o diagramas de Causa y Efecto.
Establece que los diagramas de causa y efecto como herramienta para asistir los grupos de trabajo que se dedican a mejorar la calidad. Cree que la comunicación abierta es fundamental para desarrollar dichos diagramas. Estos diagramas resultan útiles para encontrar, ordenar y documentar las causas de la variación de calidad en producción.

Otro trabajo de Ishikawa es el control de calidad a nivel empresarial (CWQC). Este enfatiza que la calidad debe observarse y lograrse no solo a nivel de producto sino también en el área de ventas, calidad de administración, la compañía en sí y la vida personal. Los resultados de este enfoque son:
1. La calidad del producto es mejorada y uniforme, se reducen los defectos.
2. Se logra una mayor confiabilidad hacia la empresa.
3. Se reduce el costo.
4. Se incrementa la cantidad de producción, lo cual facilita la realización y cumplimiento de horarios y metas.
5. El trabajo de desperdicio y el retrabajar se reducen.
6. Se establece y se mejora una técnica.
7. Los gastos de inspección y pruebas se reducen.
8. Se racionalizan los contratos entre vendedor y cliente
9. Se amplia el Mercado de operaciones.
10. Se mejoran las relaciones entre departamentos.
11. Se reducen la información y reportes falsos.
12. Las discusiones son más libres y democráticas.
13. Las juntas son mas eficientes.
14. Las reparaciones e instalación de equipo son más realistas
15. Se mejoran las relaciones humanas.
La filosofía de Ishikawa se resume en:
• La calidad empieza y termina con educación.
• El primer paso en calidad es conocer las necesidades de los clientes.
• El estado ideal del Control de Calidad es cuando la inspección ya no es necesaria.
• Es necesario remover las raíces y no los síntomas de los problemas.
• El control de calidad es responsabilidad de toda la organización.
• No se deben confundir los medios con los objetivos.
• Se debe poner en primer lugar la calidad, los beneficios financieros vendrán como consecuencia.
• La Mercadotecnia es la entrada y éxito de la calidad
• La Alta Administración no debe mostrar resentimientos cuando los hechos son presentados por sus subordinados.
• El 95% de los problemas de la compañía pueden ser resueltos con las 7 herramientas para el control de la calidad.
• Los datos sin dispersión son falsos.
Practicar el Control de Calidad es desarrollar, diseñar, manufacturar y mantener un producto de calidad que sea el más económico, el más útil y siempre satisfactorio para el consumidor.
4. Philip Crosby
Crosby es un pensador que desarrolló el tema de la calidad en años muy recientes. Sus estudios se enfocan en prevenir y evitar la inspección se busca que el cliente salga satisfecho al cumplir ciertos requisitos desde la primera vez y todas las veces que el cliente realice transacciones con una empresa.
En 1979 se crea la fundación Philip Associates II Inc. la cual se le considera una firma líder en consultorías acerca de la calidad. Se basan en la creencia de que la calidad puede ser medida y utilizada par mejorar los resultados empresariales, por esto se le considera una herramienta muy útil para competir en un Mercado cada vez más globalizado.
Crosby tiene el pensamiento que la calidad es gratis, es suplir los requerimientos de un cliente, al lograr cumplir con estos logramos Cero Defectos. En las empresas donde no se contempla la calidad los desperdicios y esfuerzos de más pueden llegar del 20% al 40% de la producción. Para lograr Cero Defectos promueve catorce pasos los cuales son:
1. Compromiso de la dirección
2. Equipo para la mejora de la calidad
3. Medición del nivel de calidad
4. Evaluación del costo de la calidad
5. Conciencia de la calidad
6. Sistema de acciones correctivas
7. Establecer comité del Programa Cero Defectos
8. Entrenamiento en supervisión
9. Establecer el día "Cero defectos"
10. Fijar metas
11. Remover causas de errores
12. Dar reconocimiento
13. Formar consejos de calidad
14. Repetir todo de nuevo
Suscribirse a:
Entradas (Atom)